Monday, it’s an AC unit that goes out. Tuesday, you walk in only to find a worn roof with an annoying leak. Wednesday comes, and the pipe system bursts, and you spend the rest of the week trying to fix that mess. Whenever any of these things need repairing, they fall into the lap of the facility manager.
Over the years, new technologies have been introduced to lessen the challenge of managing a facility, including Computerized Maintenance Management Systems (CMMS). CMMS have several different functions, including:
- Equipment Data Management: Storing key maintenance data, including processes, warranties, and technical documentation.
- Preventive Maintenance: Preventive care scheduling that preserves the life of the equipment used to manage the facility.
- Labor: The labor component of a CMMS gives managers the ability to manage their human capital resources more efficiently.
- Work Order System: Phone calls, spreadsheets, and meetings become obsolete when using a CMMS.
- Scheduling/Planning: Work order generation, prioritization, and scheduling of tasks.
- Vendor Management: Syncing with vendors to maximize those relationships and improve facility efficiency.
- Inventory Control: Inventory integrity that saves time, money, and preserves the bottom line.
- Purchasing: Triggers that give management an accurate read of what’s in stock and what needs to be ordered.
- Capital Planning: CMMS can track costs and provide historical data, allowing managers to project their needs and manage the facility while adhering to capital planning goals.
- Asset Tracking: Tracking physical and human assets through bar codes, RFID, and other technologies.
A CMMS can be one of the most powerful tools in a facility manager’s arsenal, but in too many cases, it’s the most underutilized. They’re huge investments – so why aren’t more companies using them to the fullest?
Gaining the Trust of Your Staff:
The first step in getting the most out of your CMMS is taking the power away from it – and giving it to your staff. Staff paradigms can significantly deter the consistent use of a CMMS. Most facility managers are comfortable using tried and true methods, including phone calls, pencils, notes, and spreadsheets.
“Involving the staff that will be expected to use CMMS and assuring them that it’s being implemented to make their lives easier, not monitor their activities, will make your staff more willing to accept it.”
– Maintenance Connection
They view CMMS as a threat that can be used to monitor their performance as opposed to a tool that can enhance it.
In other cases, facility managers and their subordinates are afraid that time spent trying to understand the various nuances of a CMMS will take away from their primary duty of maintaining their facility.
Empowering your staff is the first step; using your CMMS is the final step. But the one in between may be the most crucial step: TRAINING.
The lack of adequate training keeps managers from fully utilizing a CMMS. They’ll be much more apt to use the system when properly trained. This translates into increased staff efficiency and more substantial ROI for your organization.
“Flagship implemented a robust CMMS solution at 13 nationwide locations for a major auto manufacturer and provided training to key staff members.”
– Don Toole, SVP of Sales and Marketing
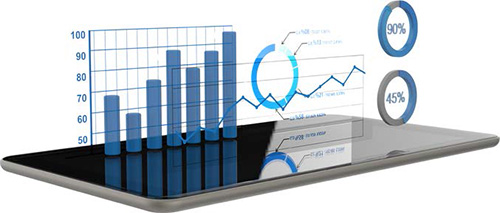
Download Now!
Take the Unleashing the Power of Your CMMS white paper with you! Download a PDF version now.
Download PDFThe Benefits of a CMMS System:
Increased Efficiency: With a CMMS in place, the workflow drastically improves, and the staff is free to move and operate far more efficiently. There’s no more guesswork about where the bottleneck will be and how to solve the day-to-day challenges, as a CMMS captures historical data and allows managers to plan accordingly.
Better Control of Your Inventory: An excellent way to understand how firm of a grasp a facility manager has on their facility is to start a conversation on inventory levels. Suppose this person has difficulty communicating where their inventory levels stand and how they’re being managed and maintained. In that case, it’s a safe bet that other parts of the operation are in just as much, if not more, trouble. A CMMS provides inventory control features that can add a much-needed layer of integrity to this critical piece of the facility’s mix.
Improved Productivity: With a CMMS in place, productivity increases exponentially. Face-to-face communication is no longer necessary, as mobile devices and synced workstations give each team member an accurate assessment of the facility’s needs, allowing them to plan accordingly.
Positive Impact on Workplace Safety: When routine maintenance isn’t performed, it puts the staff at risk. If a staff member is injured, it can have a negative impact on an organization’s bottom line due to insurance costs and decreased productivity during their absence. CMMS can manage the equipment’s maintenance schedule and protect the most important asset any organization has: its people.
Reduction in Wasteful Hours: Implementing a CMMS can greatly reduce maintenance and repair-related overtime for facility managers.
Workload Balancing: Documented workload balancing information can be stored within a CMMS. This information can be used to prepare for peak times of the year and prevent unplanned expenditures, including overtime and outsourcing fees. This feature also helps deliver a clear, concise report to stakeholders with regard to the performance of their facility and where improvements can be made.
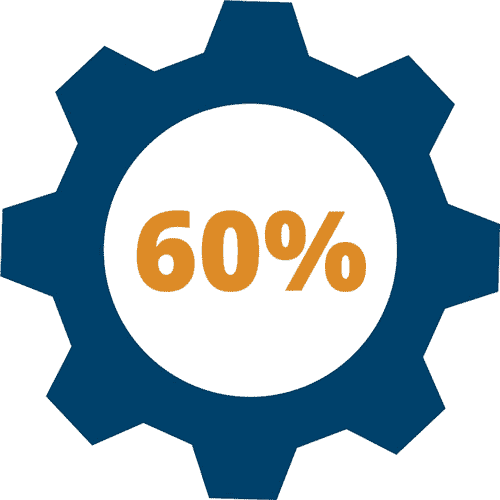
“60% of organizations that successfully implement CMMS see improved work scheduling and labor efficiency.”
– Maintenance Connection
Not All CMMS Platforms Are Created Equal
Just like all facilities are not created equal, all CMMS are not created equal. A CMMS is essential, but what’s even more important is ensuring you have the right one in place. The most common mistake organizations make is using a CMMS that does not fit their environment, leading to staff not utilizing the system. Before making this investment, spend time with your team assessing your facility. Based on those findings, invest in a solution that addresses your primary areas of need.
There are several things to consider, including the following:

- Size of Your Business: Take time to understand the size of your company. Is your company one that needs all the bells, whistles, and extra features? Or will a solution that offers maintenance, scheduling, and work order capabilities better suit you?
- Types of Users: Occasionally, facility managers must collaborate with finance, accounting, and other departments. Make sure your CMMS choice gives all the necessary parties the ability to communicate effectively.
- Technology: Does the CMMS offer a mobile component? This is important to know, as so much of facility management is impacted by mobile technology. How scalable is the solution, and how can it evolve with the needs of your business? Your organization is a living entity that will grow and change over the years. You’ll need a CMMS solution that can do the same.
Download Now!
Take the Unleashing the Power of Your CMMS white paper with you! Download a PDF version now.
Download PDFWork Order Segmentation
To fully leverage the potential of a CMMS, it’s crucial to segment work orders by areas of need. Knowing where the work was needed, capturing that data, and adding it to a historical repository gives users the ability to plan work better and manage the facility. From an accounting and expense perspective, this also helps track those areas so that proper financial allocations can be made when budgeting periods come.
“66% of facilities that use a CMMS reported improved work order processing.”
– Maintenance Connection
CMMS also comes with hierarchal features that aid in decision-making and prioritize work orders based on severity and potential impact of delays in responding. Is it mechanical, electrical, or a combination of the two? With a CMMS in place, you’ll be able to address the nature of the need and respond accordingly.
Understanding the Life of an Asset
Here’s a scenario: You’re charged with managing a facility that houses accounting, finance, marketing, sales, and a host of other departments needed to make your organization go. You come in one summer morning and notice the temperature is much warmer than usual, so you move toward the thermostat, thinking the system must have been shut off overnight.
You switch the thermostat setting on and wait for the office to cool before the other occupants arrive. Minutes turn into an hour, and as the temperature rises even higher, you realize your HVAC unit has gone out.
If you contact a repair vendor to evaluate the situation, they may inform you that if you had done regular and preventive maintenance, which you can track using a CMMS, you wouldn’t have to incur these unwanted expenses. That’s one of the many virtues of a CMMS. It provides you with a means to accurately assess and track the life of your assets and take appropriate actions to preserve them. True, purchases will need to be made, but understanding where you are regarding making those purchases and the role a CMMS plays in that process should be emphasized.
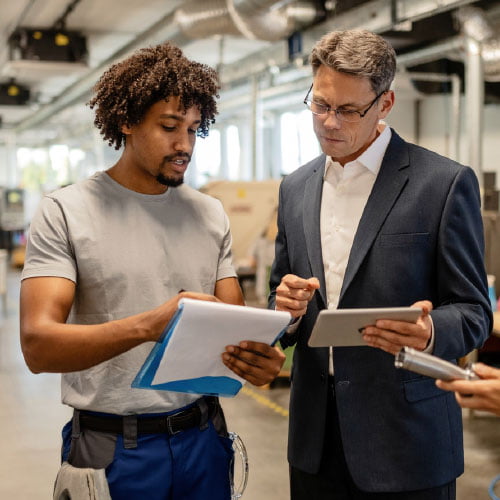
Going Mobile
With the technological advancements we have today, it’s no surprise that almost everything is going mobile, including facilities. If you’re going to integrate a CMMS into your environment, it’s important that this solution can run efficiently on mobile devices. This includes tablets that are becoming increasingly prevalent in today’s facility environments.
Connectivity can be an issue when dealing with mobile devices. Making and maintaining connections can be a serious hassle with so many layers of concrete and dense materials that are less cooperative with wireless technology. This is especially true of secure areas where access and reception may not always be the best.
With that said, when choosing a CMMS, be sure it can be used offline during periods when access to the internet may be interrupted. This will build a more stable environment and help maintain data integrity.
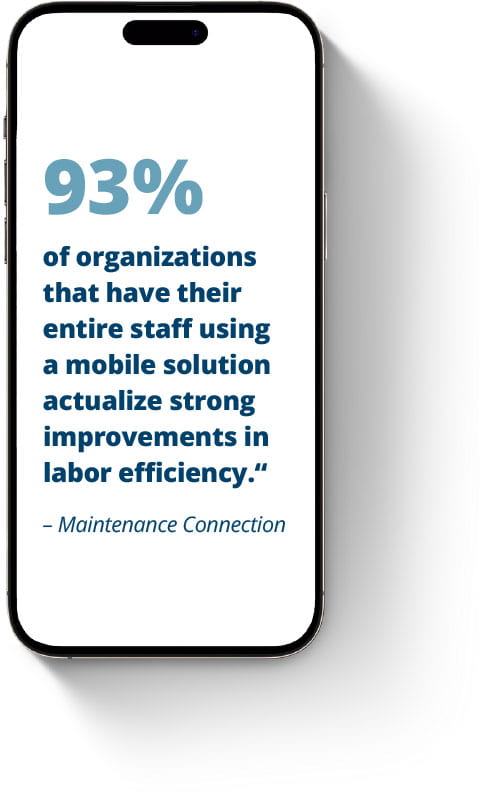
The Biggest Payoff of All
For years, facility managers have labored in a cycle of reactivity:
- A piece of machinery needs repairs
- Employee hours need to be increased
- Inventory levels have been improperly managed
- Work orders unexpectedly need to be processed
Throughout the course of each day, facility managers react to the situations at hand. With a CMMS in place, they can dramatically shift from a reactive to a preventive environment. By proactively addressing issues, you will experience a significant reduction in downtime and an increase in overall efficiency. When your facility becomes preventive, you take control and deliver true value to your shareholders. You’re able to plan your day more suitably, and your business can now prepare for emergencies that would have previously disrupted operations. Being preventive also gives your organization a competitive advantage and positions you to serve your internal and external customers better. Moving toward building a preventive environment instead of operating in a reactive mode is necessary, as those who have made the change report significant year-to-year cost savings.
Download Now!
Take the Unleashing the Power of Your CMMS white paper with you! Download a PDF version now.
Download PDFCMMS Implementation Improves Operations
The Challenge
- Multiple locations across 12 states
- No fully functioning CMMS platform for shared or collected data
- Relied on phone calls, emails, and spreadsheets for preventive and corrective maintenance
- Higher use of sub-contractors making information inconsistent and procedure flow difficult
- Lack of knowledge for capital decisions and strategy
- Previous facilities maintenance provider had been onsite for 7 years with no implementation completed
The Solution
- Turned to Flagship for our experienced team and proven procedures
- Implemented Intuition-CMMS Tenant Request System within the first 8 weeks
- Within 12 weeks, completed inventory conditions assessment and tagging for all locations
- Conditions assessments were ranked and categorized in the following 6 weeks
- Onsite customer training completed at each site to maximize utilization of CMMS
The Outcome
- Within 7 months, Flagship completely implemented both the desktop and mobile versions of Flagship Intuition CMMS
- Over 3,000 assets were tagged and updated in the system
- Data shared of critical parts inventories were now readily available and visible across all locations
- Within the first year, a 5-year capital planning analysis was generated
Conclusion
Integrating a CMMS into your environment and adequately utilizing it is the key to taking your facility to the next level. This is a significant decision that should be taken seriously. Every industry could benefit from the assistance of a reputable facilities services vendor familiar with various CMMS systems and their peculiarities. These professionals are trained in the diverse nuances of facilities and are up to date on the latest CMMS technologies. They also have the requisite skills needed to survey and report key findings on your facility that you might not otherwise be able to uncover. Armed with this information, you’ll be able to make informed decisions about your future capital expenditures.
In many cases, the necessary infrastructure and investment are in place, but the CMMS still needs to be fully utilized. This could be due to a lack of training, an unwillingness to learn or adapt, or other reasons. Partnering with a facilities services provider who can communicate the value of a CMMS and provide adequate training is essential.
87% of facilities outsource at least one part of their maintenance operations.
Receiving instructions and 800 numbers may be helpful, but having a provider with a clear vision of how to derive value from the CMMS investment is absolutely crucial. When you outsource, capital planning and asset management become far more manageable, and you begin to understand better your facility’s needs and how to address them.
Download Now!
Take the Unleashing the Power of Your CMMS white paper with you! Download a PDF version now.
Download PDFSubscribe Now!
Stay up to date with the latest facility management tips and news.