For nearly a century, this client has been a leading supplier of premium and luxury cars and vans. Its vehicles are manufactured in 17 countries and distributed all over the world. Headquartered in Europe, the company also operates a network of facilities across the United States. As the organization continues to grow, it seeks to provide pleasant, safe, and resource-friendly mobility to people everywhere.
The Challenge
Over time, the client has come to rely on third-party vendors to perform a number of facility services, including cleaning, engineering, and maintenance. Since they are responsible for serving multiple clients, many third-party vendors offer limited availability and little to no quality control. As a result, the client has experienced extended periods of downtime and elevated operational risk.
Faced with these challenges, the client turned to Flagship Facility Services for its expertise in process improvement and total quality management.
The Solution
To kick things off, Flagship completed a detailed review of the work being performed by third-party vendors. The team identified several opportunities to transition work away from contractors and self-perform certain janitorial tasks and facility repairs.
Flagship began carrying out many of the jobs that were previously dispersed between vendors, including exterior window cleaning, cleaning supply management, HVAC preventive maintenance, MEP repair and maintenance, and Fire-Life-Safety monthly compliance activities. As an extension of the client team, Flagship ensures both quality performance and on-time execution.
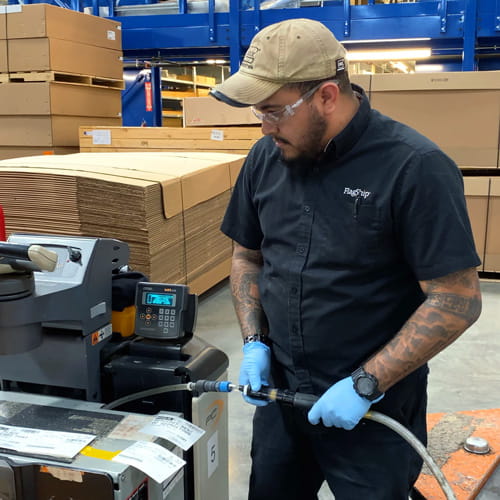
The Outcome
Simply by insourcing key facilities management tasks, the client has significantly increased its operational efficiency. Not only does Flagship have an intimate understanding of the client’s business, but the team is leveraging its know-how to create new value and reduce risk across the organization. By partnering with Flagship, the client has minimized its downtime and supply usage, resulting in considerable cost savings. The company has also greatly improved its in-house communication and collaboration skills.
Flagship’s strategic approach and commitment to continuous improvement were crucial to the success of this initiative. Flagship hosts daily meetings with the client to analyze performance and explore additional opportunities for optimization.
A proud partner to the client team, Flagship looks forward to driving positive change within the organization for many years to come.
Download Now!
Take the Flagship Serves as the Driving Force Behind an Automotive Client’s Insourcing Initiative with you, download a PDF version of it now.
Subscribe Now!
Stay up to date with the latest facility management tips and news.